Ball mills and
Rod mills are the most commonly used grinding equipment in concentrators .
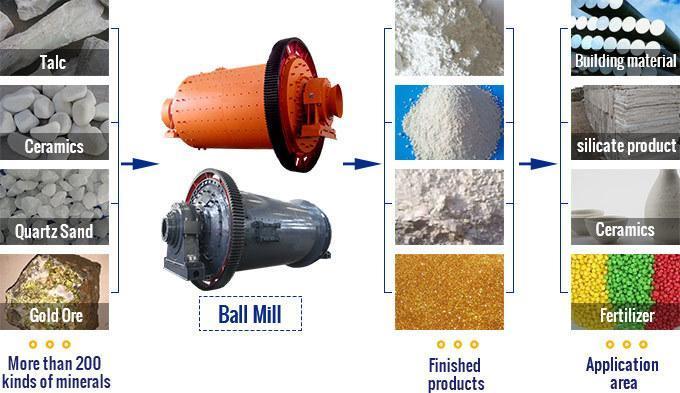
But for many people, the ball mill and the rod mill are like a pair of "twins", both of which are long cylindrical grinding equipment. It is not easy to distinguish from the shape alone, but if we delve deeper, we will find that there are many differences between them.
It is the difference in these details that determines the tendency to purchase grinding equipment.
Generally, we can distinguish according to its equipment structure, grinding medium, discharge method, grinding medium filling rate, equipment performance and scope of application, etc., and select the ideal type of grinding equipment for the concentrator.
Difference 1. Equipment structure
On the surface, it is difficult for many people to distinguish between a ball mill and a rod mill, but in fact, there is a difference in the proportion of the shape of the cylinder. Generally, the ratio of the length to the diameter of the barrel of the rod mill is maintained between 1.5-2.0, and the inner surface of the liner on the end cover is in a vertical plane state. The ratio of the length to the diameter of the barrel of the ball mill is relatively small, usually equal to 1 or slightly greater than 1. In addition, the rotating speed of the rod mill barrel is generally lower than that of the ball mill of the same specification, so the grinding medium in the rod mill barrel is usually in a cascading state.
Difference 2. Grinding media
According to the equipment name, rod mills usually use steel rods with a length greater than 500mm as grinding media, while ball mills use steel balls with a diameter of less than 100mm as grinding media. The difference in grinding media is also a significant difference between the two grinding equipment.
Difference 3. Discharging method
Different discharging methods are suitable for different grinding processes. Choosing a reasonable discharging method will improve the grinding efficiency of the mill to a certain extent.
For ball mills, we can choose overflow type and grid type discharge methods according to different production requirements. The slurry level of the grid type ore discharge is low, and qualified products can be discharged in time, but sometimes the grid plate is easy to be blocked and maintenance is inconvenient; while the overflow type discharge is easy to manage and maintain, but the discharge level is high, and the slurry is in The residence time in the mill is long, and the processing capacity per unit volume is low. The rod mill does not have a grid plate. There are two main types: overflow type and open type. The diameter of the hollow shaft at the discharge end is larger than that of the ball mill of the same specification.
Difference 4. Filling rate of grinding medium
Grinding medium filling rate refers to the percentage of grinding medium that occupies the volume of grinding equipment. Different grinding methods, equipment structures, operating conditions and medium conditions require the filling rate of the grinding media to maintain an appropriate range, too high or too low will affect the grinding effect. According to a summary of practice, the filling rate of ball mills is usually 40%-50%, while that of rod mills is 35%-45%.
Difference 5. Equipment performance
The grinding medium of the rod mill is in linear contact with the ore, so it has a certain selective grinding effect, only has the grinding power, the product size is more uniform, and the over-crushed ore particles are less. In addition, the processing capacity and grinding effect of the rod mill are greatly affected by the particle size of the ore. In rough grinding, when the product particle size is 1-3mm, the processing capacity of the rod mill is greater than that of the ball mill of the same specification; when used for fine grinding and the product particle size is less than 0.5mm, the grinding effect of the rod mill is far less than the specification Ball mill. While the ball mill is in point contact with the ore, it has both impact and grinding force, and the product particle size is finer. In addition, the ball mill has strong adaptability to materials, high production capacity, easy fine grinding, and significant energy saving, but its over-crushing phenomenon is more serious.
Difference 6. Scope of application
In the gravity separation or magnetic separation process of tungsten-tin ore and other rare metal ores, rod mills are often used to grind materials in order to prevent over-grinding and dust pollution. In the second-stage grinding process, the rod mill is usually used as the first-stage open-circuit grinding, with larger production capacity and higher efficiency. When processing low-hardness and brittle materials, the rod mill can completely replace the cone crusher for fine crushing. The ball mill is not suitable for the gravity separation process in metal ore beneficiation because of the fine grinding materials and prone to over-crushing. However, it is widely used in other beneficiation processes.
The above is the specific analysis of the ball mill and the rod mill. I believe it can help you to choose the right grinding equipment to a large extent. Choosing the right grinding equipment is a systematic work. The various factors are related to each other and restrict each other. It is recommended to consider all aspects and make reasonable choices in order to obtain the ideal grinding effect.
Who we are?
Shanghai CLIRIK Machinery Co.,Ltd. has been committed to the field of fine and ultra-fine powder grinding machines for 20 years.
CLIRIK has a first-class manufacturing base with standardized and intelligent production lines.
CLIRIK's professional R&D, sales, installation and after-sales teams have provided door-to-door services to more than 100 countries and regions.
Which models can be selected for processing ultra-fine powder except ball mill and rod mill?
How to get the latest quotation?
You can leave a message online or contact CLIRIK directly:
Email: sales@clirik.com
WhatsApp: +8613512155195/+8613917147829