Ultrafine powder usually refers to particles with a particle size of micrometer or nanometer. Compared with the bulk of conventional materials, it has a larger specific surface area, surface activity and higher surface energy, so it exhibits excellent optical, thermal, electrical, magnetic, catalytic and other properties. As a kind of functional material, ultrafine powder has been widely studied in recent years, and has been more and more widely used in various fields of national economic development.
Coated calcium carbonate powder
However, due to the unique agglomeration and dispersion problems of ultrafine powder, many excellent properties have been lost, which severely restricts the industrial application of ultrafine powder. Therefore, how to avoid the agglomeration failure of ultrafine powder has become a difficult problem in the development and application of ultrafine powder. By coating the superfine powder to a certain extent, the surface of the particles can obtain new physical, chemical and other new functions, thereby greatly improving the dispersibility of the particles and their compatibility with other substances. The surface coating technology effectively solves the problem of agglomeration of ultrafine powders.
The mechanism of superfine powder surface coating
Regarding the coating mechanism, it is still under study and there is no conclusion yet. The main points of view are as follows:
-
· Coulomb electrostatic attraction mechanism. This view is that the coating agent has a charge opposite to the surface of the substrate, and the coating agent particles are adsorbed to the surface of the coated particles by Coulomb attraction.
-
· Chemical bond mechanism. A strong chemical bond is formed between the substrate and the coating through a chemical reaction, thereby generating a uniform and dense coating layer.
-
· Supersaturation mechanism. This mechanism is based on crystallography. It is believed that when a heterogeneous substance exists at a certain pH value, if the solution exceeds its supersaturation, a large number of crystal nuclei will be generated immediately and deposited on the surface of the heterogeneous particle to form a package. Cladding.
Surface coating method of superfine powder
1. Mechanical mixing method.
Using mechanical forces such as extrusion, impact, shearing, friction, etc., the modifier is evenly distributed on the outer surface of the powder particles, so that various components can infiltrate and diffuse into each other to form a coating. At present, the main applications are ball grinding method, stirring grinding method and high-speed air impact method. The method has the advantages of short processing time, easy control of the reaction process, and continuous batch production, which is more conducive to coating powder particles with various resins, paraffin substances and fluidity modifiers. However, this method is only used for the coating of micron-sized powders, and the powders are required to have a single dispersibility.
2. Solid phase reaction method.
Several metal salts or metal oxides are fully mixed and ground according to the formula, and then calcined, and the superfine coating powder is directly obtained through solid-phase reaction.
3. Hydrothermal method.
In a closed system of high temperature and high pressure, water is used as a medium to obtain a special physical and chemical environment that cannot be obtained under normal pressure conditions, so that the reaction precursor is fully dissolved and reaches a certain degree of supersaturation, thereby forming a growth element, and then Nucleation and crystallization make composite powder. The advantages of the hydrothermal method are as follows: the synthesized core-shell nanopowder has high purity, narrow particle size distribution, controllable crystal composition and morphology, complete crystal grain development, light agglomeration, and a dense and uniform shell of the product. , The prepared nano-powder does not require post-crystallization heat treatment.
4. Sol-gel method.
First, the modifier precursor is dissolved in water (or organic solvent) to form a uniform solution. The solute and the solvent undergo hydrolysis or alcoholysis to obtain the modifier (or its precursor) sol; then the pretreated coated particles Uniformly mixed with the sol to uniformly disperse the particles in the sol, the sol is processed to be transformed into a gel, and calcined at a high temperature to obtain a powder coated with a modifier on the outer surface, thereby realizing the surface modification of the powder. The coated composite particles prepared by the sol-gel method have the advantages of high purity, good chemical uniformity, small particles, narrow particle size distribution, etc., and the technology is easy to operate, simple in equipment, and capable of preparing various functional materials at lower temperatures. , It has obtained good applications in the preparation of magnetic composite materials, luminescent composite materials, catalytic composite materials and sensors.
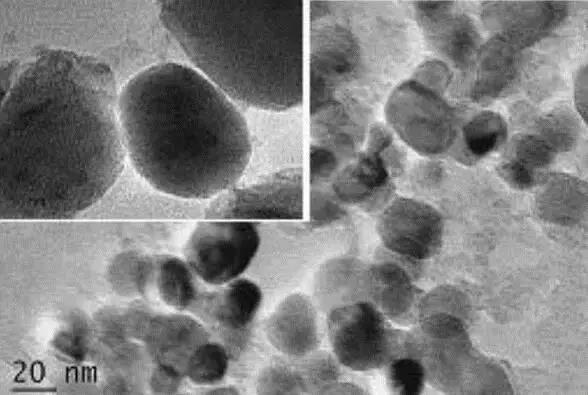
Graphene coated rare earth doped nano oxide
5. Precipitation method.
Adding a precipitating agent to the solution containing powder particles, or adding a substance that can initiate the formation of the precipitating agent in the reaction system, causes the modified ions to undergo a precipitation reaction and precipitate on the surface of the particles, thereby coating the particles. Precipitation reaction coating often involves coating inorganic oxides on the surface of nanoparticles, which can conveniently control the concentration of metal ions in the system and the release rate and dosage of the precipitant, and is particularly suitable for coating micro-nano powders with inorganic modifiers.
Nano-magnesium hydroxide composite powder material coated on the surface of fly ash hollow microbeads
6. Heterogeneous coagulation method (also known as "hybrid flocculation method").
A method proposed based on the principle that particles with opposite charges on the surface can attract each other and condense. If the diameter of one kind of particles is much smaller than the diameter of another kind of charged particles, then during the aggregation process, the small particles will be adsorbed on the outer surface of the large particles to form a coating layer. The key is to modify the surface of the particles or directly adjust the pH of the solution to change the surface charge of the particles.
7. Microemulsion coating method.
Firstly, the ultrafine powder to be coated is prepared by the tiny water core provided by the W/O (water-in-oil) type microemulsion, and then the powder is coated and modified by microemulsion polymerization. Compared with other preparation methods of nanomaterials, the preparation of nanomaterials by microemulsion method has the following characteristics: (1) The particle size distribution is narrow and easier to control; (2) Because the surface of the particles is coated with one layer (or several layers) of surfactant The molecules are not easy to coalesce, and the obtained organosol has good stability and can be stored for a long time; (3) The reaction is carried out under normal pressure, the reaction temperature is relatively mild, the device is simple, and it is easy to realize.
8. Non-uniform nucleation method.
According to the theory of the LAMER crystallization process, the non-uniform nucleation and growth of the modifier particles on the coated particle matrix are used to form the coating layer. This method can precisely control the thickness and chemical composition of the coating layer. In the non-uniform nucleation coating, the mass concentration of the modifier is between the non-uniform nucleation critical concentration and the critical saturation concentration. Therefore, the non-uniform nucleation method coating is a kind of coating that occurs between the non-uniform nucleation critical concentration and the uniform nucleation critical concentration. Precipitation coating between the critical concentration of phase nucleation.
9. Electroless plating method.
It refers to the process of metal precipitation by chemical method without applying electric current. There are three methods: displacement method, contact plating method and reduction method. The electroless plating method is mainly used for covering the surface of ceramic powder with metal or composite coating to realize the uniform mixing of ceramic and metal, thereby preparing cermet composite materials. The essence is that the metal ions in the plating solution are reduced by the reducing agent to metal particles and deposited on the surface of the powder under the catalytic action. It is an autocatalytic oxidation-reduction reaction process, so a certain thickness of metal coating can be obtained, and the thickness of the coating is uniform. , Porosity is low.
10. Supercritical fluid method.
It is a new technology that is still being researched. In the case of supercritical, reducing the pressure can lead to supersaturation, and can reach a high supersaturation rate, so that the solid solute crystallizes out of the supercritical solution. Since the crystallization process is carried out in a quasi-homogeneous medium, it can be controlled more accurately. Therefore, solid deposition from supercritical solutions is a promising new technology that can produce fine particles with a very small average particle size and control their particle size distribution.
11. Chemical vapor deposition method.
At a relatively high temperature, the mixed gas interacts with the surface of the substrate to decompose certain components in the mixed gas and form a metal or compound coating on the substrate. It generally includes 3 steps: generating volatile substances; transporting volatile substances to the precipitation zone; chemically reacting with the substrate to produce solid products.
12. High energy method.
The methods of coating nanoparticles with infrared, ultraviolet, gamma rays, corona discharge, plasma, etc. are collectively referred to as high-energy methods. High-energy methods often use some substances with active functional groups to coat the surface of nanoparticles under the action of high-energy particles.
13. Spray thermal decomposition method.
The process principle is to spray a mixed solution of several salts containing the required positive ions into a mist, send it into a reaction chamber heated to a set temperature, and generate fine composite powder particles through the reaction. In this process, from raw material to product powder, there are 4 basic links including solution preparation, spraying, reaction and collection.
Silica coated zirconium diboride-silicon carbide composite powder
14. Microencapsulation method.
A surface modification method that covers the surface of the powder with a homogeneous film with a certain thickness. The size of the microcapsules usually prepared is 2 to 1000 μm, and the thickness of the wall material is 0.2 to 10 μm. Microcapsules can change the appearance and shape of the capsule core material without changing its properties, and can also control the release conditions of the core material; it can isolate the substances that react between phases for long-term storage; it can play a role in toxic substances. Concealment. Microencapsulation technology has been widely used in the pharmaceutical, food, coating, adhesive, printing, catalyst and other industries.
Concluding remarks
The selection of surface coating technology should be comprehensively considered based on the characteristics of the core powder and coating material and the application of the modified composite powder. With the development of science and technology, the ultrafine powder coating technology will be further improved, and it is expected to produce multifunctional, multi-component, and more stable ultrafine composite particles, which will open up broader application prospects for composite particles. At present, the surface coating mechanism of ultrafine powder and the preparation of ultrafine powders with better performance through a variety of coating methods will be the future research and development direction in this field.